Goldpine
Mechanised Cable Harvesting : Mechanisms of Innovation
Tucked away in the Moutere Forest, the Mechanised Cable Harvesting (MCH) team of seven spend their days working at Tasman Pine. Owned by Nathan Taylor, Hamish Matthews, and Ross Wood, the business also has a duplicate team working at another site – both fully mechanised swing yarder crews with cable extraction.
Ten years ago, the opportunity arose for Nathan and Hamish to be part of a Tasman-based forestry business alongside Ross, who ended up being a great mentor for the pair. “We were lucky to have a really good mentor in Ross, to be able to point us in the right direction – showing us what works, the broadening our areas of innovation and what other parts of the industry that we can learn from. Between me and Hamish, we’re very hands-on; we take great pride in working with our team where we can, but we still try to be hands-on with the tools. We love being out in the forest because, like today, it’s a beautiful place to be. Aside from the hands-on stuff, we work together to ensure the smooth day-to-day running. It’s a really good business, I thoroughly enjoy it.”
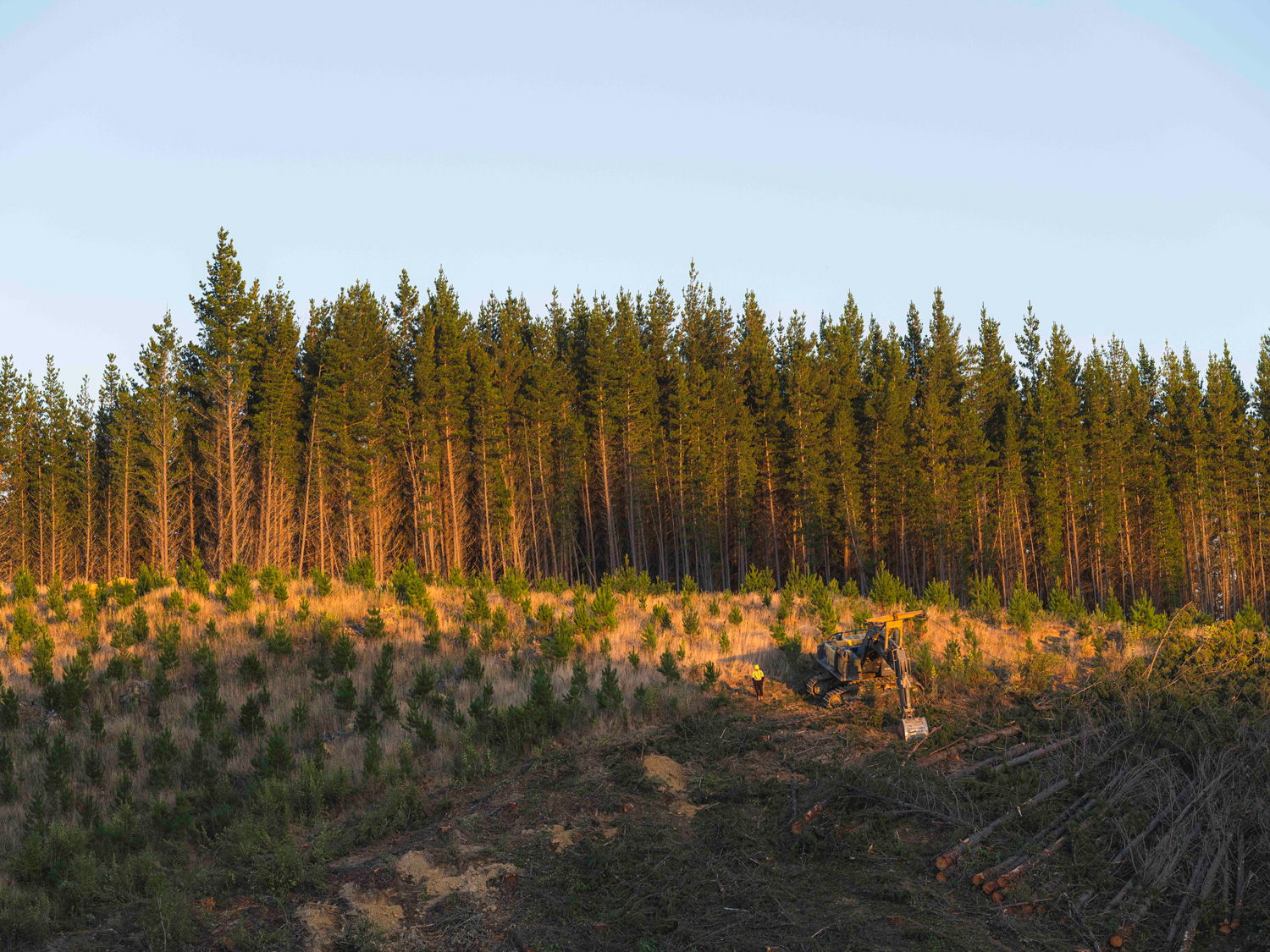
When Nathan left school, he got the opportunity to go and work for Goldpine at the Golden Downs Yard.. At that stage, everything was done manually, running around with a pole and marking out the posts to certain lengths before cutting them with a chainsaw. Goldpine later implemented mechanisation for efficiency, to minimise waste and reduce unnecessary labour. Over the years, technology in forestry has increased tenfold, with systems that not only help to increase productivity but also promote health and safety.
“A good ten to 15 years ago, there were high rates of accidents within the forestry industry. However, there’s a real move to mechanisation. Chainsaws have been replaced by highly efficient excavators with log processors attached to maximise the value of the tree, along with log haulers fitted with motorised grapples capable of extracting trees off steep hillsides. We have rope-operated grapples with remote cameras, all with the same purpose: to remove people from high-risk tasks. Probably the biggest change has been the introduction of tethering; this gives us the ability to work a felling machine on slopes that traditionally would have been felled with a chainsaw. The way we look at it is, we put people in cabs; that way, we are doing everything we can to keep our people safe,” Nathan said.
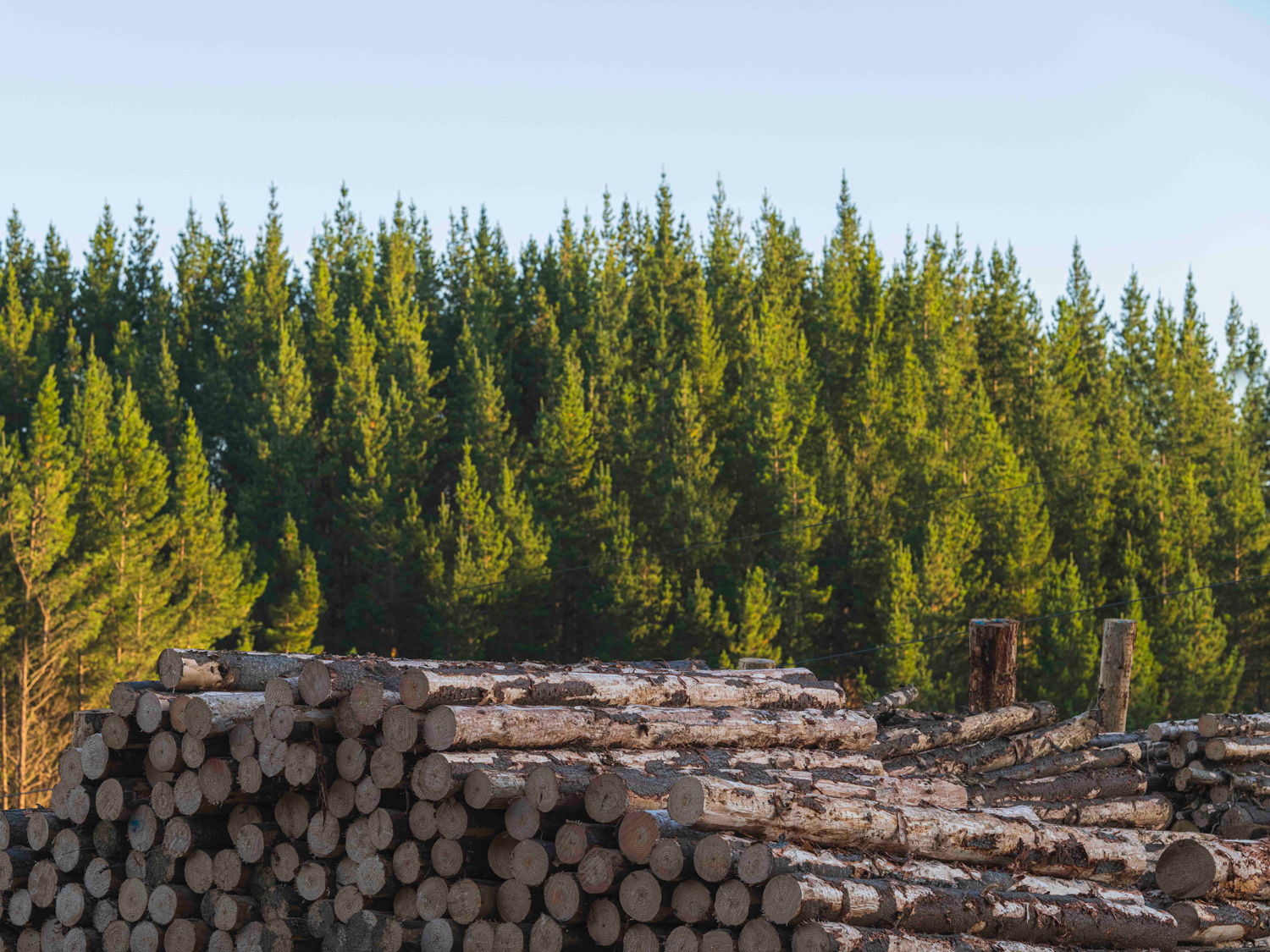
“Tree felling used to be the highest-risk job – felling trees manually with a chainsaw; the statistics have proven that most of the people who have been hurt in forestry are the ones using a chainsaw to cut down trees. So by being in a cab, you minimise the risk. The second dangerous thing was hooking the trees up with strops; now we’ve got a grapple, we don’t have anyone running around the hillside.. So, the safety factor has improved for the business and the forestry companies. For those high-risk jobs, we don’t have to worry about them anymore because the guys are safe,” Hamish added.
The forestry industry has been given a bad reputation, especially with all of the slash that was found in waterways, in the Gisborne and Hawke’s Bay regions during the floods last year. Nathan addressed the issue by showcasing that their business is focused on sustainability and best practices when it comes to their workers, the end-user, and the environment.
“The whole process starts at the felling face; you get one opportunity to cut a tree and put it in the best place. By doing this, it flows onto helping the hauler laying the trees at the right angle, which then helps with extracting them efficiently. We all want to get the most out of the trees. It’s a plus-plus for every part of the supply chain – we get paid for what goes on the truck, we don’t get paid on what gets left on the hill,” Nathan said.
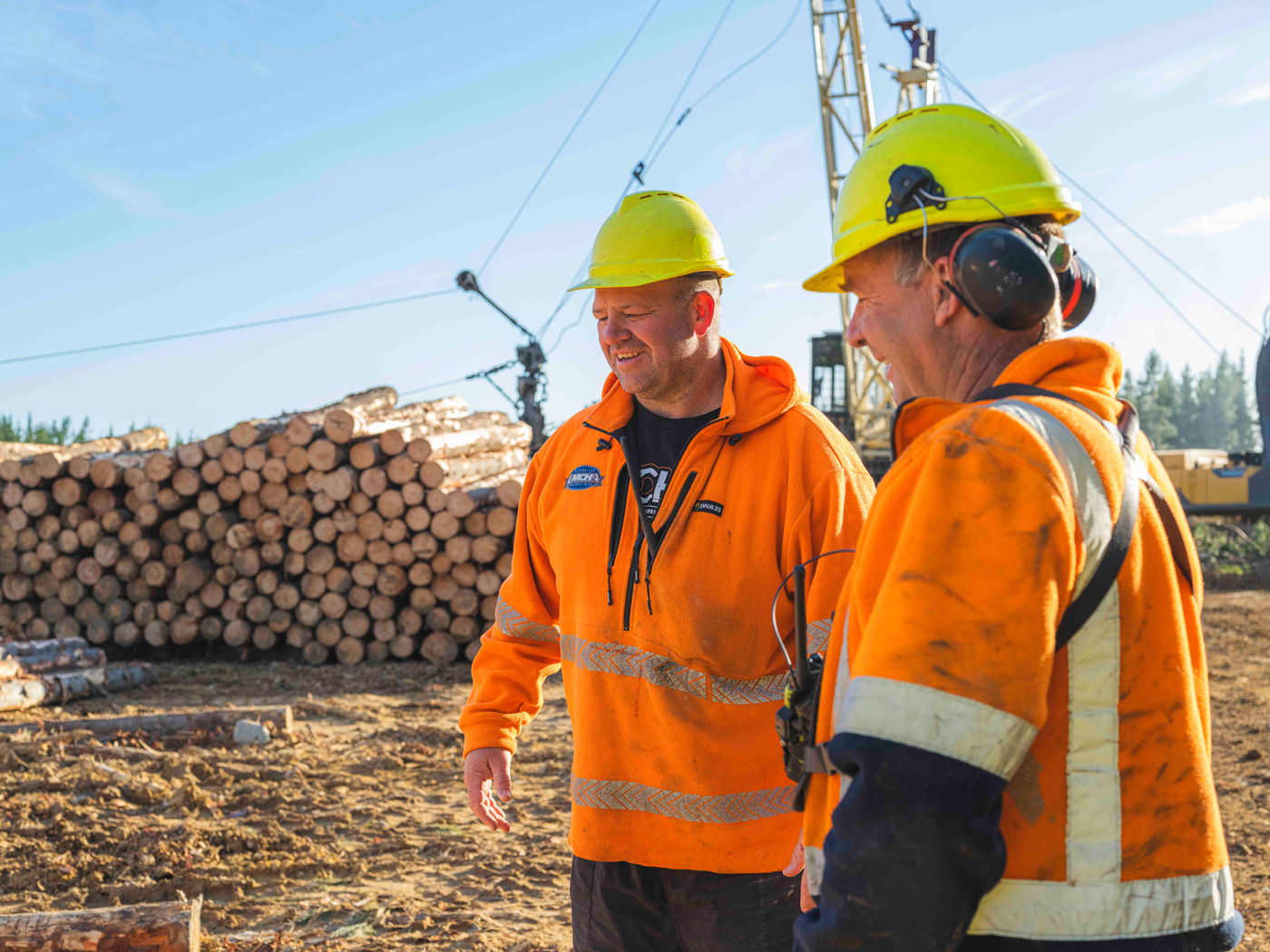
MCH uses a camera system, which was built locally, attached to the hauler grapple. It has great picture quality, so this assists in helping locate bunches along with making sure there is little waste left in the harvest area, which helps with slash control.
“With the TimberPro, it’s got the QB4400 fixed felling head on it. What it can do is grab the tree, cut it, hold it straight up in the air, swing it around, and place it nicely on the ground without any breakage . This helps in retrieving the smaller end of the tree that would typically be broken and left to rot in the forest. That’s where a lot of Goldpine product comes from – post wood and CTLs [cut-to-length posts],that’s the high-quality grade of domestic timber you pay big dollars for. In the machine, there’s a diameter sensor. So, as it’s grabbing each tree, it will tell you roughly how big it is in tonnes; you can measure the exact amount which makes it more effective for the hauler pulling those great big piles. We also do CTLs for Goldpine, which is up to 20% of our workload per day. These little beauties are cut in half, then they are quartered, and become the high-quality product that Goldpine sells,” Hamish said.
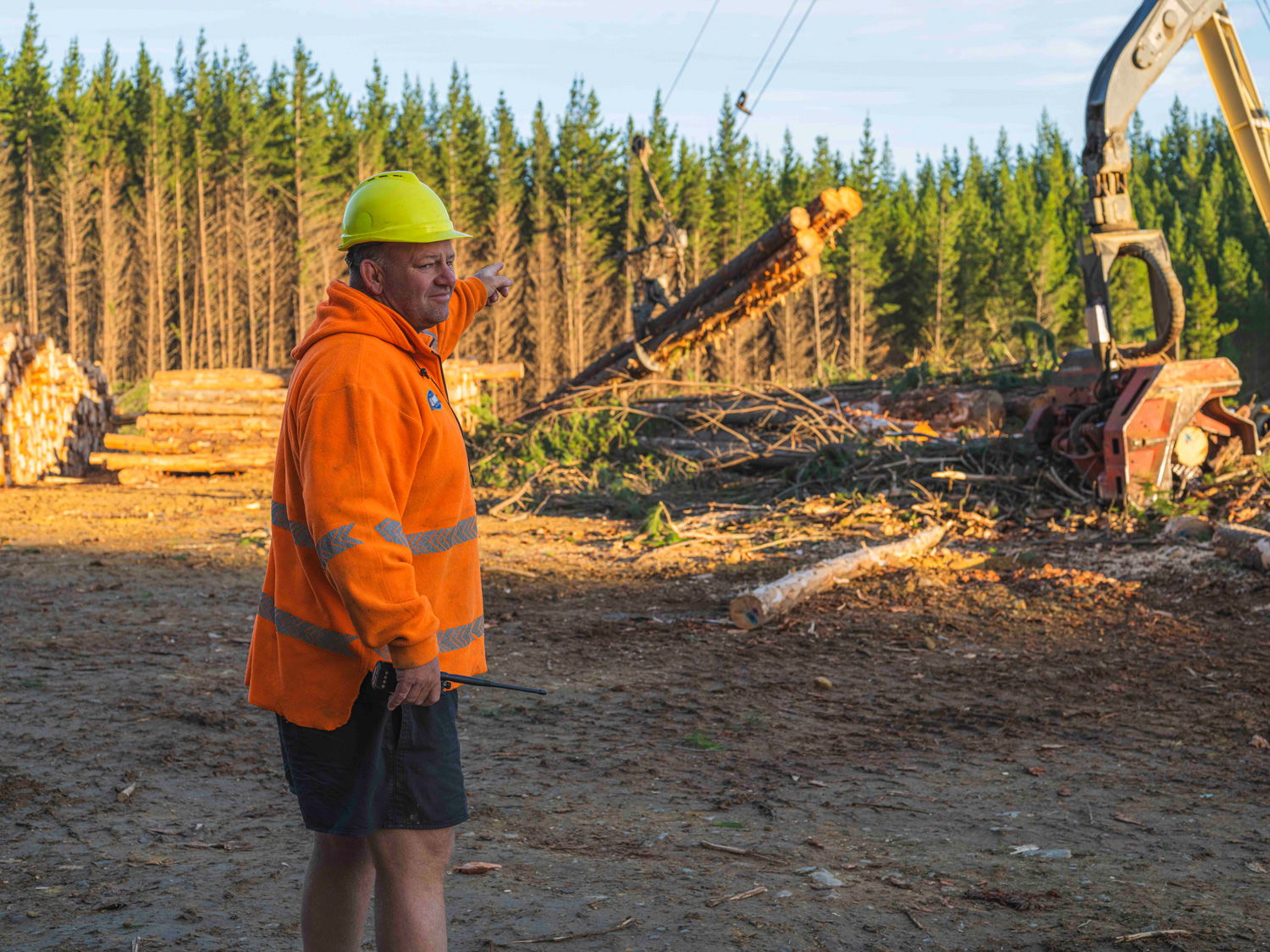
“We have had the team at Goldpine come out to look at what we do, including our ability to be able to generate a lot of the smaller timber that is valuable for them when making posts. We’ve got a good relationship with Goldpine, and we’re always happy to accommodate them at the site.” Nathan added.
“We’re really lucky in smaller communities like ours where forestry brings a lot of ongoing work across the whole supply chain, and it’s great having a forest at our backdoor for recreational activities. We keep an eye on the latest technology and stay ahead of innovation. We pride ourselves on being innovative loggers and are always looking to capitalise on opportunities.”
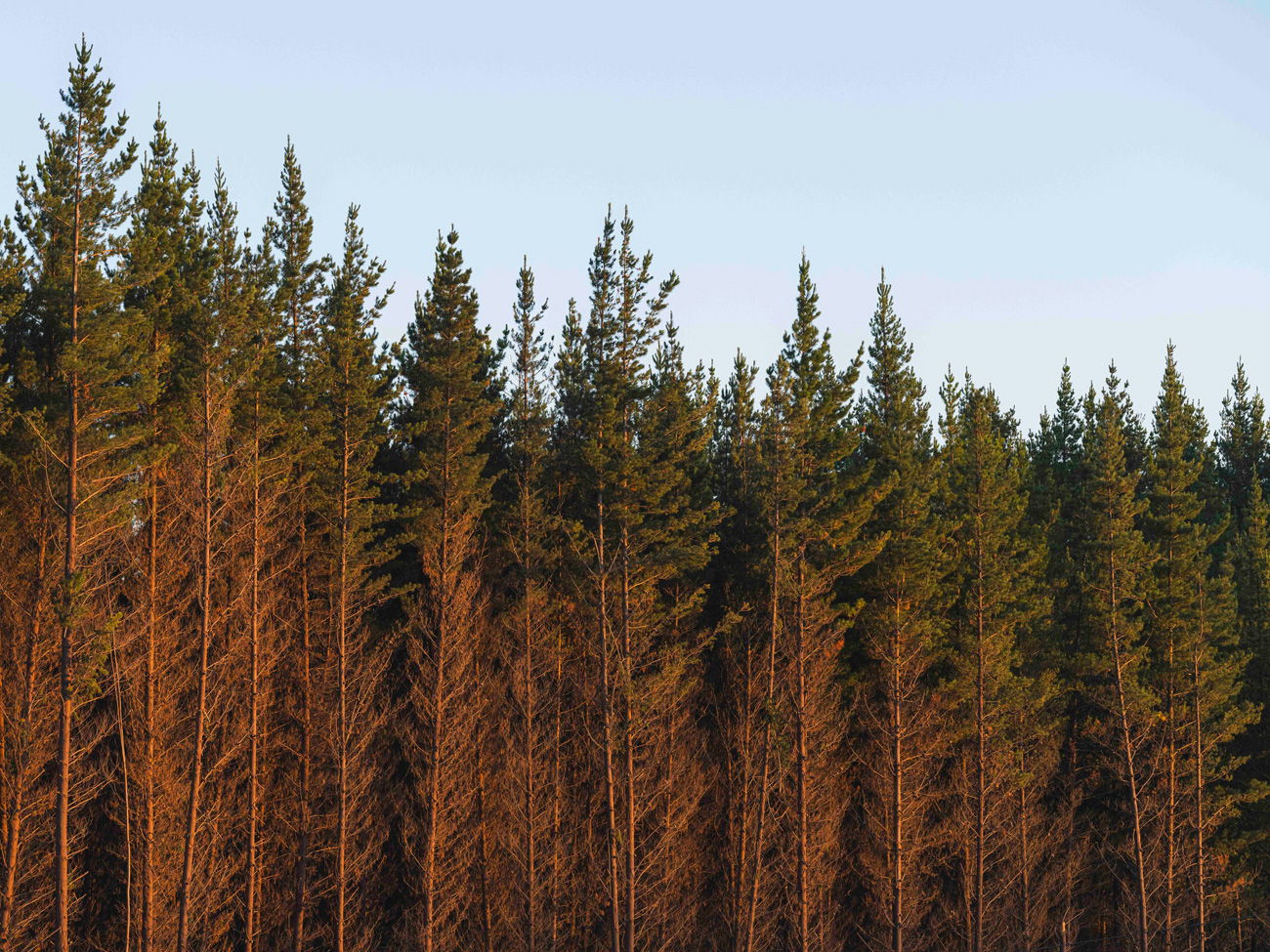
“We can have all the fanciest machines in the world and have million-dollar haulers and shiny equipment, but it’s all about the guys and girls that are sitting in the seat. We take great pride in having good people and are a family-first business. Some of our team members have been working with us for a long time, and we’re very lucky to have them.”
MCH’s relationship with Tasman Pine is a great one, with Nathan highlighting the business’s enthusiasm for health and safety and environmental compliance. They take on board feedback from the MCH team and are very collaborative. MCH is currently working for PF Olsen too, having also worked for OneFortyOne in the past, and likes to maintain good relationships with the managers and forestry companies within the region.
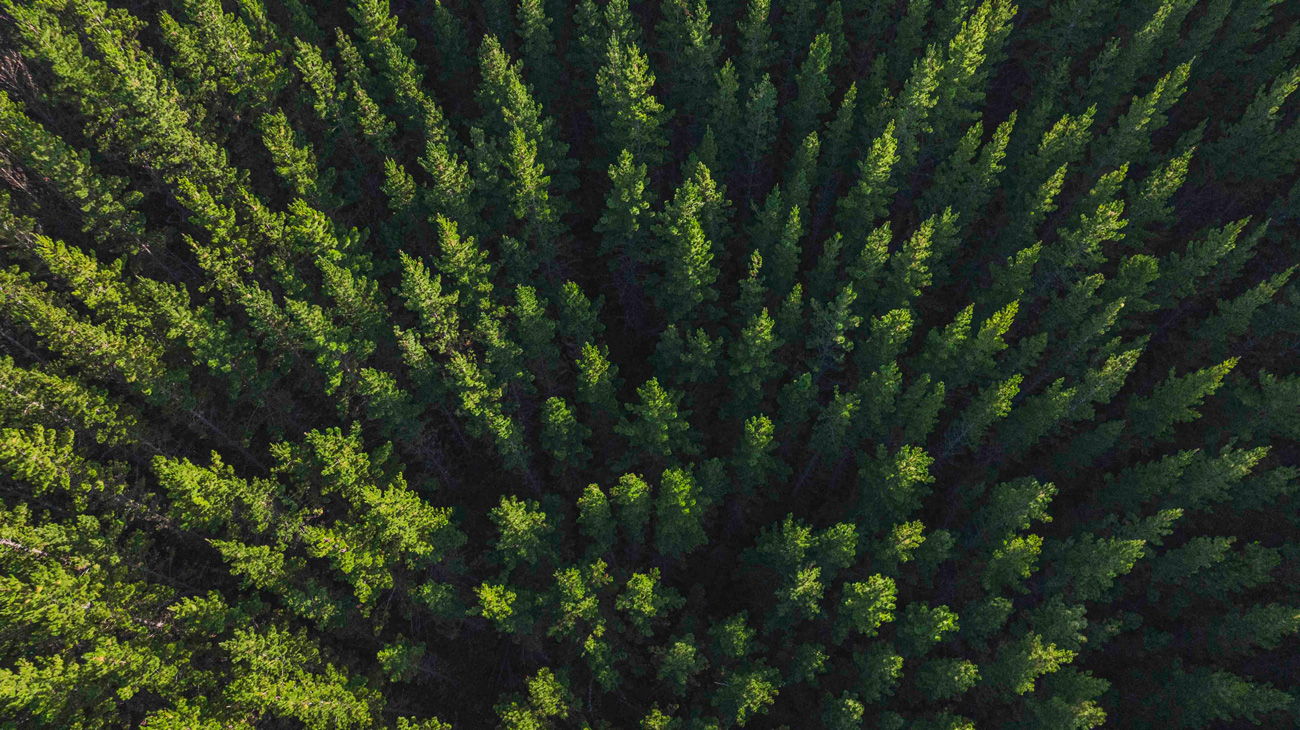
For those wanting to get into forestry, Nathan said there’s nothing like having a good mentor and not being afraid to ask for advice. The number of employment opportunities within the field is endless.
“We haven’t got a lot of younger people coming through, so it’s about making it an exciting industry to be in, one that will attract and retain people. Forestry is a sustainable industry and it does a lot for small regions. Most people in forestry are down-to-earth and are willing to roll up their sleeves, they’re just good people to be around. I would recommend the forest industry - it’s a good place to be,” Nathan concluded.
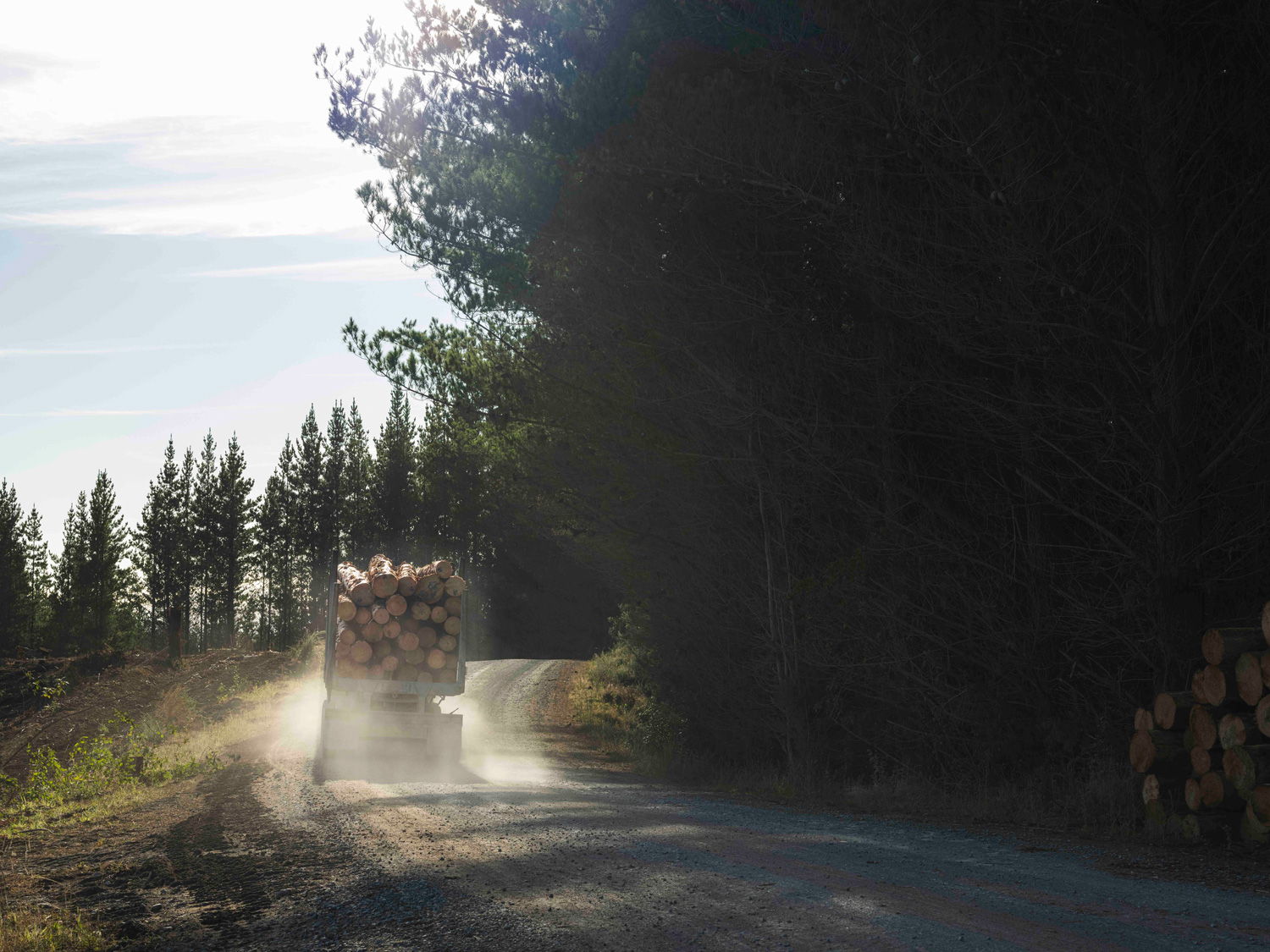